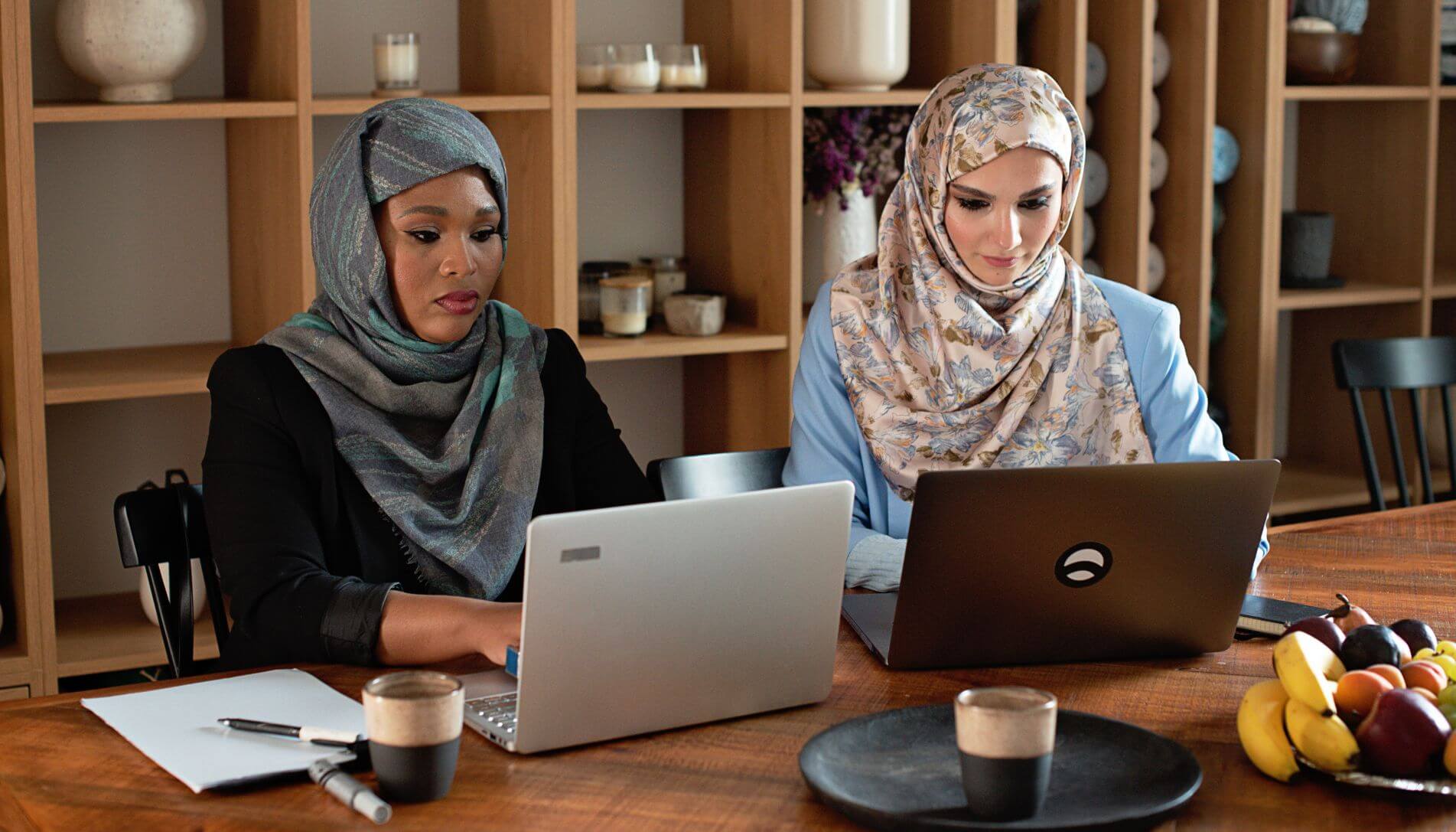
Introduction
Lean can be as diverse and complex as those who make up the teams that use it. To learn more about Lean and Lean certifications, make sure to see our Lean Six Sigma online courses.
The 5 Lean management principles
It is worth noting that Lean has been adapted to fit very niche contexts in many varied industries. Lean management principles detailed below may vary in number and thought depending on which industry you work in and which projects Lean is applied to.
Some versions of Lean may detail up to as many as 9 Lean principles, but for this example, we’ll stick with the most basic five Lean principles:
1. Identify value
This first principle requires Lean practitioners to deduce what a customer wants from a product. Often customers won’t have a solid idea or may be unable to articulate what they want. This may be due to a lack of industry knowledge, a lack of technical knowledge, or a desire to use new, untested technology.
There are several methods that can be used to discover value. We can use our industry knowledge of consumers, software, and technology to create better solutions. Or we can gather relevant information through surveys and interviews.
2. Map the value stream
Next, Lean practitioners must map each of the steps it will take to deliver the product. This helps teams understand which processes may produce waste. Once found, the team finds ways to eliminate those steps or reduce them as much as possible.
Value streams are often displayed visually and without a lot of technical jargon so that all involved can get a clear and concise idea of what is required to create the finished product.
3. Create flow
Once the most obvious sources of waste are eliminated, the next step is ensuring the processes that create value can proceed without delays or disruptions.
This requires that staff be trained in multiple skills, creating cross-functional teams, which can help balance the workload among all staff.
Creating adequate workflow prevents bottlenecks and delays in development. It can also improve office morale by keeping everyone working at a steady pace without harsh deadlines and sudden changes to development.
4. Establish pull
A pull system limits inventory and work in progress (WIP) items by only producing enough to meet customer demand. This prevents tasks, staff or components from sitting idle, waiting for someone to come around and begin the next phase of development.
Pull systems have been proven to be effective and are used in many modern project management methodologies.
The most well-known is the Kanban system – In a pull system, completed tasks are placed in a pool of resources. When a developer finishes a task, they then look at the pool and pull out the next highest priority task they can complete.
5. Seek perfection
Lean teaches that there is always a process to be improved or a wasteful to be eliminated. Organisations that implement Lean can only do so successfully by creating an environment of learning and experimentation that promotes personal and professional improvement.
Lean and Agile
It is common for Lean and its variants to be referred to by the umbrella term Lean Agile.
Agile refers to any management method that aligns with the ideas first outlined in the Agile Manifesto, written to improve those processes and existing methods deemed inadequate for use in software development.
Agile describes three primary concepts common to all contemporary Agile methods: an iterative approach to development, short feedback loops, and a disciplined project management process.
While you may think that Lean is derived from Agile, it is, in fact, the opposite – Agile is rooted in Lean.
Lean manufacturing
The concepts that together create what we know of as Lean Manufacturing first originated in 1940’s post-war Japan, decades before Agile made its introduction.
During this time, demand for many products in the Japanese economy was low, so automotive manufacturer Toyota determined that actual sales rather than production targets should drive work schedules.
This meant avoiding costly over-production by building products to order, pulling them onto the market rather than target-driven push manufacturing.
The term Lean Manufacturing was first coined in 1988 by engineer John Krafcik in his article Triumph of the Lean Production System. It was later elaborated upon by James Womack, Daniel T. Jones, and Daniel Roos in the early ‘90s.
The basic Lean Manufacturing principles do not differ very much from the principles used in Lean management today:
- Determine value
- Map the value stream
- Establish a workflow
- Establish a pull system
- Focus on perfection.
What is different are the finer details such as “What is value?” or “What creates waste?” In manufacturing, waste is created by worn-out machinery, transportation costs, poorly engineered components, or excess inventories.
In modern industries, waste may refer to bloated software with additional features that do not provide value to users or an online registration procedure that is convoluted and time-consuming.
Agile principles
At a very basic level, Lean and Agile are almost indistinguishable.
In Agile software development, teams apply an iterative approach to software delivery. Developers first create a minimum viable product which, though it may lack many planned features, can be put into work and immediately start generating value for customers.
Similarly, Lean encourages teams to deliver fast by managing workloads and limiting the amount of WIP (work-in-process) to improve focus and reduce development time. Both Lean and Agile teams manage flow by working in cross-functional teams and delivering one iteration at a time.
Agile promotes short feedback loops so that developers only do work that meets the latest business requirements.
Lean also encourages this in its definition of waste – if you’re making something that doesn’t meet your customers’ needs, it is a waste. Short feedback loops help eliminate activities that do not provide value.
Agile methods rely on disciplined governance that encourages frequent review and learning. This approach helps developers discover valuable insights after each release that can then be applied to improve the quality of future iterations.
The Lean principle of “Build Quality In” encourages businesses to automate any process prone to human error so that developers can focus on more complex tasks. This automation, troubleshooting, and consistent delivery process helps Lean teams continuously refine and optimize their development processes.
Implementing Lean management
Adopting Lean into your development model isn’t as simple as learning the Lean principles. It’s a lengthy process that might fail without adequate guidance and preparation. You may want to consider soliciting the help of professional change managers to help ease the transition to Lean.
But in a more general case, if we do not consider change management issues, there is still the difficulty of deciding which of the many lean tools to use and adopt. Lean includes dozens of tools, methods, and techniques, the relevance of which are very situational. Implementing lean requires that organisations make some very important decisions (hopefully based on a lot of research!).
Implementing Lean always has an associated risk. Unfortunately, there are no specific tools for the selection and prioritisation of methods during implementation. To mitigate the risk of implementing Lean in your business or organization, it’s important that all key staff are adequately trained to the level of Lean suitable to their position within the organizational hierarchy. Each level of Lean Six Sigma certification, for example, corresponds to staff duties within project development. To learn more, make sure to see our selection of Lean Six Sigma online courses and in-house training.
It may benefit organisations to assess the value of Lean from a cost/benefit/risk perspective and ask the following questions:
- What is the benefit of this lean technique and how difficult is it to achieve? (Is it worth doing this? Is it worth risking failure?)
- Does this lean technique benefit the sustainability of the change intervention? (Would it have long-term benefits?)
While the decision to adopt lean is usually a top-down decision, always bear in mind that sudden change is likely to meet resistance. Lean is, fundamentally, an organisational culture. Adopting Lean requires a change management process that fosters positive outcomes through coaching and mentoring as opposed to merely directive top-down change.